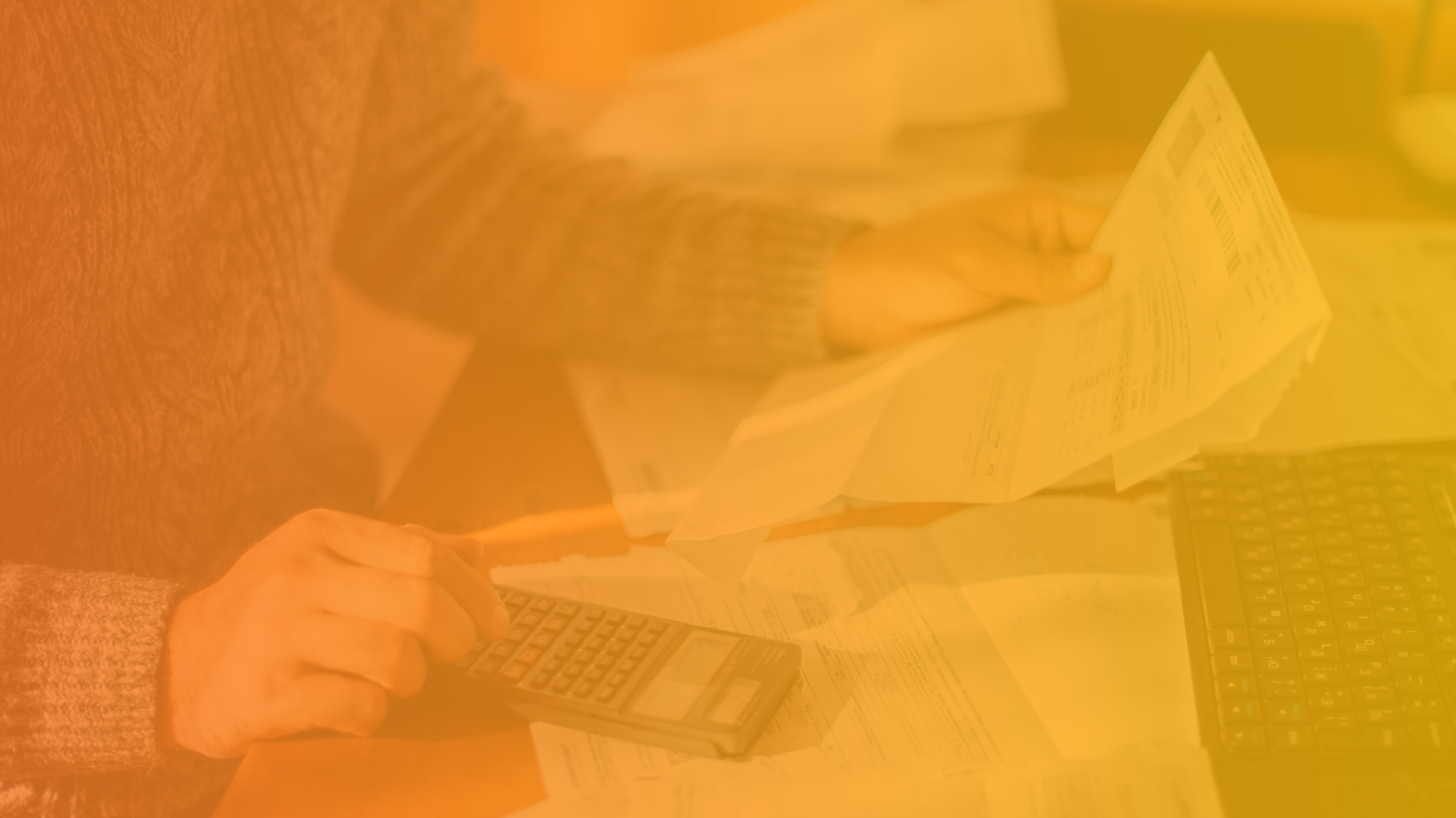
Frequently asked questions
-
Magnatech is a non-intrusive, custom designed, retrofit energy saving system which is attached to a boiler’s fuel supply pipe within 1 metre of entry into the boiler.
It consists of an array of mixed polarity neodymium magnetic materials, the configuration of which is determined by the parameters of the boiler. The diameter, thickness and material of the pipe are also factors that determine the number, size and positioning of the super strength anisotropic sintered units.
-
The system works on any industrial, commercial, or domestic sized boiler using gas, oil and liquid petroleum gas (LPG). Also Magnatech is transferable so if you upgrade boilers then Magnatech can be removed and installed on the new system.
-
The pipe size is a factor we consider, as the magnetic configuration and its penetration through the pipe walls can be rendered less effective if the pipe diameter increases above 6 inches.
-
Factors which affect the efficiency of the Magnatech System include the flow rate, the diameter of the fuel pipe, the material it is made from and the configuration of the pipework. The kWh output does not affect the results. The Magnatech System has been installed onto boilers ranging from 20 kWh up to 3500 MW output with fuel consumption reduction ranging from 6% to 20+%.
-
The Magnatech System uses an non-homogeneous magnetic field to condition hydrocarbon molecules, allowing them to be able to interact more readily with oxygen.
The result is a more efficient combustion which creates a higher flame temperature.
This reduces unburned fuel, increases fuel efficiency, and lowers carbon emissions and means your thermostat set temperature is reached using less fuel.
-
The maximum lead time to optimum performance is between 1-4 weeks depending on the material and diameter of the supply pipe. A steel pipe takes longer (4 weeks) than a PVC / copper pipe (6 hours). This period is required to allow the magnetic field to saturate into the pipework.
This process causes no harm or damage to the pipework or the boiler.
-
It doesn’t! Conditioned fuel achieves a hotter flame with less fuel consumption, thus reducing both the amount of fuel and boiler activity required to achieve the pre-set thermostatic temperature. This in turn reduces the carbon emissions produced by the boiler.
-
A constant base line of consumption, taken from recent utility bills or smart meter readings is required to accurately determine the results utilising a minimum of 3 months data. A mutually agreed fuel consumption baseline is determined based on time and fuel demand parameters which can be compared with future similar parameters for utilising International Performance Measurement & Verification Protocol (IPMVP) and/or Heating Degree Day (HDD) calculations. We are happy to assist in this process where required.
Following installation of the Magnatech System and once optimum fuel conditioning performance is achieved, data is collected for a minimum of 3 months. This data is then compared to the agreed baseline data using industry standard heating degree days HDD calculations.
-
As it is installed onto the fuel supply pipe, the system does not meet the boiler or any of its parts. Additionally, the Magnatech units are shielded to direct their powerful magnetic field into the pipework so that it does not negatively affect the boiler or any potentially sensitive nearby devices. The temperature increase in the flame is a small percentage and well within the tolerances of any boiler.
Hamworthy and Worcester Bosch, two of the world’s largest boiler manufacturers, have confirmed in writing that the Magnatech system will have no negative effects on their boilers. We have installed our units on thousands of boilers dating back over 15 years and have never had any reported issues. We do recommend that the boiler’s air/fuel mix is checked during the next servicing cycle or after 6 weeks from the date of installation to optimise fuel savings. This is something the service engineer carries out as a part of a standard maintenance check.
-
Fuel consumption can be influenced by a variety of factors, including outside temperature, the temperature of incoming water for steam boilers, for heating systems even the wind and the speed of heat loss can make a difference. Variations in production and demand, alterations to the raw material, new processes being introduced, new leakage and heating loss. The variation of calorific value (CV) of fuels, but most significantly of all are people. So, systems where there is no interference to the thermostat and where there are controlled conditions produce the most reliable results.
-
The Magnatech System is constructed within protective shielded casings which block the magnetic fields from projecting outward from the pipes, thus protecting anyone or any object from encountering the magnetic fields post-installation. All Magnatech units carry the below Health & Safety advisory:
WARNING! Very strong magnetic fields.
Take care to avoid trapping fingers when handling units.
Keep away from Pacemakers etc.
Keep away from electrical equipment.
-
The product manufacturers are ISO9001, AS 9120B and IATF 16949 certified.
-
We have case studies and detailed results from a range of installation sites available on request. (Please note - Many clients will not wish to release their data as they view this as confidential material. Magnatech only shares studies with pre-approval from the client).
-
Yes, so have we. This information relates to magnets which are sold as diesel and petrol saving devices. We are happy to explain to anyone as to why they do not work and can never work. If anyone reads of a failed Magnatech installation, please let us know as we haven’t heard of one, EVER! The Magnatech System is not a magnet in that it produces an inhomogeneous field and not a homogenous one. A homogenous field which is created by a magnet will not be able to produce the reaction required in fossil fuels.
-
Following a site survey which can be carried out virtually, a quotation is provided and ROI is usually within 6 - 30 months. Once this ROI is achieved you will benefit from consistent additional savings over the lifecycle of the product. The product loses less than 1% of its efficacy every 100 years!
Enjoy a lifetime of savings with no maintenance or ongoing costs required!